Hello from Alaska!
The utilities industry is one of the most hazardous in the world. The top hazards range from exposure to electricity & natural gas, working at heights, in confined spaces, and during extreme weather events. Despite the hazardous nature, the safety performance has continually improved over the last decade. According to the U.S. Bureau of Labor Statistics, the incident rates of nonfatal occupational injuries for utilities decreased 15% from 2.1 in 2013 to 1.8 in 2023. This is far below the average for all industries at 3.0. Despite this positive trend there’s plenty more room to reduce risk and advance along the ‘journey toward zero’ health, safety, and environment (HSE) incidents that every utility is on.
The power of root cause analysis
Having worked in the energy industry for two decades and seen accidents and have been exposed to hazards, root causes analysis (RCA) was engrained in me by the organizations I worked for and served. RCA is a powerful tool that allows organizations to dive deep into HSE incidents or recurring problems, identifying and addressing the core issues that cause them. Unlike surface-level troubleshooting, RCA goes beyond symptoms to uncover systemic weaknesses. By systematically asking questions-often using methods like the ”5 Whys” or Fishbone diagrams – RCA helps utilities implement changes that prevent issues from recurring, leading to more safe and efficient operations.
Also engrained in me was the belief that 100% of all incidents are preventable. Any business leader across this entire industry would agree and even reinforce this belief within their teams. There’s one simple equation that can help categorize identified root causes and to assist in finding solutions to prevent future incidents along the journey to zero.
Information + Human Action = Business Outcomes
All of us are tasked with creating positive business outcomes. Improved safety performance and reduction of risk are just two examples of business outcomes utilities strive to improve upon. Any business outcome is created from two key ingredients, information and human action.
However, not just any information or human action will create business value. What was considered productive work decades ago may be considered unproductive today. The best use for human action is addressing tasks that machines don’t perform as well, as safely, or as cost effectively. Likewise, the best jobs for machines are tasks that humans don’t perform as well or as effectively. The best information can be trusted to boost human (and asset) productivity, free knowledge workers from manual and error-prone steps and minimize risk. Just as human action needs to be managed to achieve business outcomes, so does information. So, the more accurate equation that is implied in this formula is that ‘management’ underpins all three components.
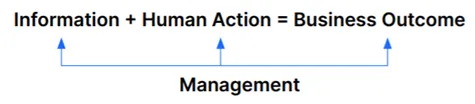
If an accident were to occur and root cause analysis was performed, examples of failures from the management of human action might be; failure in work prioritization, procedure not followed, inadequate training, poor communication, fatigue, and many more.
Performing the same exercise but for failures in information management might include outdated safety protocols, inaccurate asset documentation, poor visibility into the transaction status of spare parts, no predictive maintenance insights, emergency response information poorly communicated, and many more.
GenAI will play a key role along the journey to zero
Generative AI places information at the fingertips of humans and has close ties to the information management domain. Great AI requires great information management because the results from generative AI will be more correct and trusted when information is organized, connected, automated, and secured.
Information Reimagined with GenAI will play a key role along the journey to zero whether inadequacies in information management are identified as a root cause of an incident or whether a proactive approach to risk reduction is taken. Using an intelligent AI content assistant that puts chat-based conversational search, content discovery (ex. safety procedures, job safety analysis, emergency response plans, operating instructions, and much more), summarization, and translation at your fingertips. Trusted knowledge is available simply by asking a question and it’s this knowledge that will power improved safety performance. See OpenText Content Aviator for more detail.
About the Author, Phil Schwarz
Phil Schwarz is the Sr. Industry Strategist for Energy & Resources at OpenText. With two and a half decades of industry experience, Phil has become a trusted SME, having supported operators, EPCs, service providers, and OEMs across the entire value chain. Phil is an engineer by education and has a MBA, M.S. in Economics, M.S. in Finance, and a Graduate Certificate in Smart Oilfield Technologies. He resides in the Anchorage, Alaska area and loves to hike and enjoy the outdoors.