Lithium-ion batteries not only power everyday devices like cell phones and laptops, they are a critical part of the U.S.’ alternative energy strategy and pivot away from fossil fuels, used in everything from electric vehicles to solar panels to energy storage.
The Biden administration has been pushing to bolster the U.S.’ lithium battery production capabilities for more than a year. The effort includes funding and resources for domestic lithium mining and the end-to-end supply chain, including the processing and manufacturing of electric vehicle batteries.
The goal is to reduce the country’s reliance on foreign lithium supply and increase the nation’s energy self-sufficiency. But to get there, the U.S. will need to drastically expand its domestic lithium manufacturing base.
The National Blueprint for Lithium Batteries 2021-2030, developed by the Federal Consortium for Advanced Batteries, or FCAB, outlines the country’s plans to bolster investments in the lithium supply chain, beginning with mining and including processing and production.
With goals of improving processing, procurement and workforce development in the industry, the blueprint lays bare the Biden administration’s pathway towards a more sustainable energy future and the supply and operations needed to get there. But with little current access to the world’s lithium stock, it will be an uphill battle.
Domestically sourcing lithium is a ‘huge undertaking’
The U.S.’ only existing lithium producer is in Nevada, and the country holds an estimated 3.6% of global lithium reserves, according to the U.S. Geological Survey. The bulk of the world’s lithium production power lies in China, and consulting firm Wood Mackenzie estimates the country makes up nearly 75% of the world’s lithium-ion battery manufacturing capacity, as well as a chunk of its lithium reserves. Other lithium reserves lie largely in Australia, Chile and Argentina.
The foreign power in the industry means the U.S. must source most of its needed lithium overseas.
The global demand for lithium-ion batteries is also growing, as other nations move to combat the climate crisis using alternative energy. With that rise in demand, the market is poised to be worth $100 billion in the coming decades, said David Howell, acting director and principal deputy director of the Office of Manufacturing and Energy Supply Chains at the Department of Energy and chair of the FCAB.
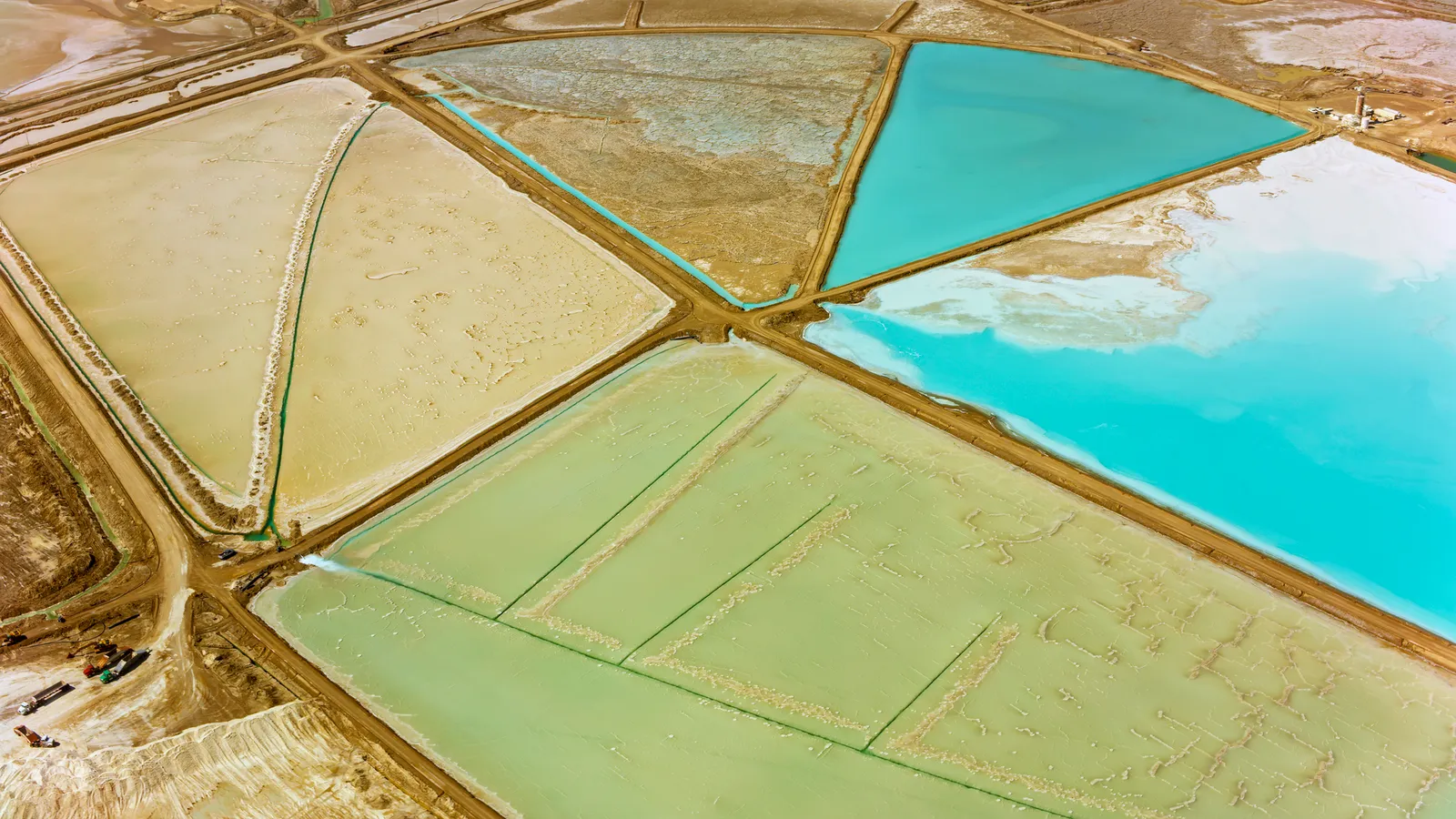
Much of that demand comes from the booming global EV market, with sales reaching historic levels last year and on track to do so again in 2022, according to the International Energy Agency. The Biden administration set a target last year that by 2030, half of new cars sold in the U.S. should be zero-emission vehicles.
The administration has also moved forward with consumer financial incentives for automakers that source critical minerals in North America. But domestic supply is nowhere close to meeting demand.
“Where is the supply? We don’t make electrode materials,” said Venkat Srinivasan, director of the Argonne Collaborative Center for Energy Storage Science at Argonne National Laboratory and deputy director of its Joint Center for Energy Storage Research. “We don’t make materials that go into the rest of the battery. We don’t process the minerals. We don’t even mine them.”
Where are the world's lithium reserves?
While trying to domestically source raw materials like lithium is a great idea, it’s a huge undertaking, said Charlie Welch, founder and CEO of battery developer ZapBatt. Starting new mining operations is an expensive and politically fraught endeavor.
“Even if we flip the switch and say the U.S. is going to do this overnight,” he said, there are a lot of hurdles including expense and environmental challenges. “It’s not easy to pull specific things out of the ground.”
Still, automakers have been under pressure to manufacture at home. The Biden administration is offering a $7,500 tax credit for electric vehicles if the battery is made predominantly made with materials extracted or processed in the U.S.
“Every car manufacturer is talking about how their fleet will be primarily electric by 2030,” said Srinivasan.
To help accelerate domestic production, the president has announced a slate of investments to shore up manufacturing. The administration awarded $2.8 billion in grants last month to boost production of EV components, such as lithium materials.
To help carry out more of these plans and investments, the government also created Li-Bridge, a public-private partnership run by Srinivasan and Argonne National Laboratory, to help reach the goals stated in the blueprint. With Li-Bridge, “the goal is to bridge the gap between the supply of batteries and the growing demand,” he said.
Li-Bridge aims to bring together industry stakeholders to collaborate on building the lithium supply chain. It has been working to align the federal government’s vision with the private sector’s, to understand bottlenecks in the industry and what must be done to meet the federal government’s goals, Srinivasan said.
To pull off the new supply chain, innovation is necessary
Still, to address capacity issues, innovation breakthroughs will be necessary. Some researchers, for example, have created batteries that use fewer critical minerals, including not only lithium but cobalt and nickel.
“There are innovative chemistries that do not use cobalt, that do not use nickel,” Howell said. “And some of these are on the market today. Lithium iron phosphate batteries use lithium, but do not have cobalt nor nickel.”
Research into new designs must happen at the same time as expanded current production, to ensure continuous improvement, Srinivasan said. “We must think about all parts simultaneously.” he noted.
“Where is the supply? We don’t make electrode materials. We don’t make materials that go into the rest of the battery. We don’t process the minerals. We don’t even mine them.”

Venkat Srinivasan
Director, Argonne Collaborative Center for Energy Storage Science at Argonne National Laboratory
Recycling has also emerged as a potential solution to meet demand. Biden's blueprint also includes plans to develop greater recycling capabilities that can capture more useful battery minerals, Howell said.
The goal in the blueprint is to create incentives for companies to achieve 90% recycling of consumer electronics, EV and grid-storage batteries by 2030.
Still, with the supply of recycled materials not expected to meet demand, other companies are looking at alternative formulations for their batteries.
“There’s often a race to invent brand new batteries, a miracle battery,” Welch said.
Welch’s ZapBatt is created with lithium-titanate technology to produce a faster-charging, longer-lasting battery. Originally developed for military use, the batteries can charge in less than 20 minutes while getting 15,000 charging cycles, he said.
Will the U.S. succeed?
To many industry observers, the U.S. government’s multifaceted approach to building a sophisticated lithium supply chain is a good start, but many challenges remain. Srinivasan is reassured by the number of small companies with hundreds of millions of dollars worth of battery manufacturing capabilities, and the auto companies establishing new battery factories in the U.S. He sees recycling companies receiving capital to start collecting and recycling cells and batteries.
“Five years ago, I used to agonize over this, thinking it’s just a bunch of R&D,” Srinivasan said. “[I thought], ‘how are we ever going to make an impact in the real world?’”
Still, while recycling and a circular economy are important, they're "not a magic bullet," said Welch. “We can barely recycle Tupperware right now."
More effort should be spent on ensuring that batteries have a long life in the first place, he said. With all the energy put into mining and acquiring scarce minerals, emphasizing a longer battery lifetime would encourage producers to make efficient use of available materials, leaning away from a “fast fashion economy for batteries."
But with big and small companies rushing to find solutions, more stakeholders are cautiously optimistic that mineral production can be scaled sustainably.
“I'm super excited. I’m more hopeful,” Srinivasan said. “I’ve never seen a time like this.”