The solar industry is about to have an escalating amount of defunct panels on its hands, and companies like Solarycle are positioning themselves to turn those panels into profit.
A study from the National Renewable Energy Laboratory in 2021 found that the total amount of defunct panels in the U.S. could reach 1 million metric tons in 2030 and 10 million metric tons by 2050.
Sensing that influx of materials, some recyclers are beginning to scale up their own solutions for panels that have reached the end of their useful life. One such startup is Solarycle, which received a $1.5 million U.S. Department of Energy grant this week to partner with NREL to explore ways to extract higher-quality materials from recycled solar panels.
That follows a $30 million series A funding round that closed last month, led by investors Fifth Wall and HG Ventures.
Suvi Sharma is Solarcycle’s CEO and a co-founder of the company, along with former Sierra Club National Program Director Jesse Simons and photovoltaic recycling expert Pablo Ribeiro Dias. Sharma recently spoke with Waste Dive about how the new funding will allow the company to double its capacity. He also said the solar industry is keen on finding paths to circularity, and he noted the public and private financing alike that’s backing companies willing to try.
The following interview has been edited for length and clarity.
WASTE DIVE: Let's start with your investment. You recently received a series A investment round totaling $30 million that was led by Fifth Wall and HG Ventures. Tell me what that investment will enable Solarcycle to do.
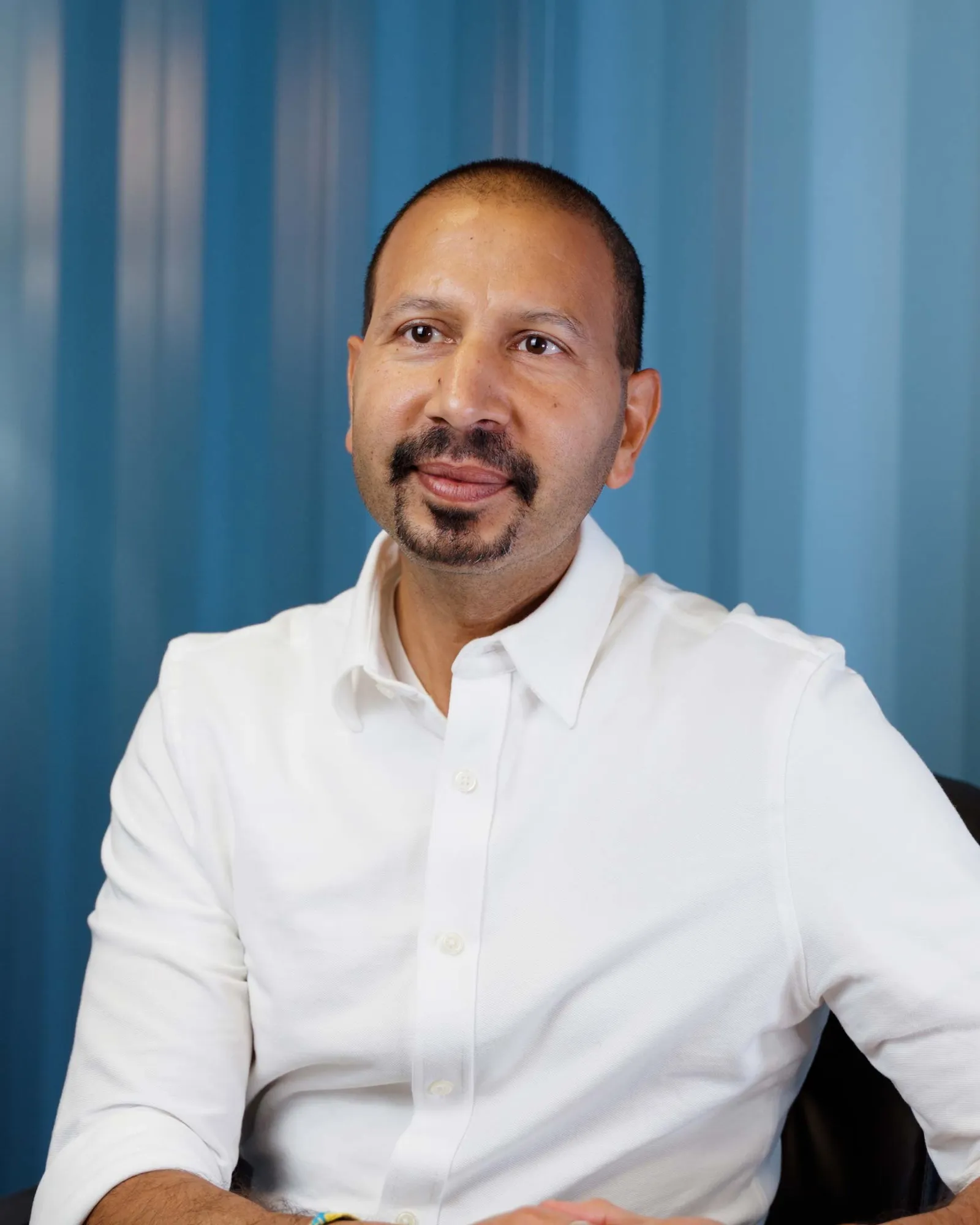
SUVI SHARMA: There's two key things that it will enable us to do. One is scale up our recycling operations — we've set up our first facility in Odessa, Texas, that's a very advanced solar recycling facility. We have a lot of R&D that's gone into that: new equipment, technology. Right now we have a capacity to be able to recycle 500,000 solar panels there and we're going to double that to a million panels per year, and also investing in some further downstream metal separation processing equipment and technologies there.
[The series A funding] allows us to expand and vertically integrate the entire soup-to-nuts recycling and extraction process for solar panels, and then also gives us capital as we need to expand additional facilities on an as-needed basis as the market for recycling solar panels expands.
Thing two is it enables us to double down and triple down on R&D. We are very focused on not only scaling recycling for solar, but developing the advanced technologies and processes and equipments that are needed to have a very cost-effective and a very efficient recycling process for the increasing number of solar products that need to be recycled.
So we're investing more in R&D, and that ranges from higher-throughput recycling and extraction processes to also starting to invest in some remanufacturing technologies. Not only are we extracting the materials out of the solar panel, but we are also purifying and remanufacturing some new materials from those so we enter those back into the solar supply chain.
How much of your end product is sold back to solar panel manufacturers at present?
Today it's zero, because what we do is we extract the raw materials. The solar panel manufacturers, what they do is they buy finished materials such as specialized solar glass or specialized frames. Today we supply into the raw material market, and then those materials get remanufactured into a final product that could go into the solar industry.
But as we evolve, we will be remanufacturing some of those products ourselves, and that will enable us then to supply those finished materials and products directly back to the solar panel manufacturers and the solar supply chain.
What's the motivation behind investing in that remanufacturing process?
Well, there's really two distinct benefits or rationales for it. The first is, as a company and for Solarcycle, we can build a more valuable and larger business. The recycling and extraction process is one value piece of the equation, but there's a lot more value as we can convert those raw materials into finished products. As you can probably imagine, as you start to add value to the materials and make finished products, there's just more value that we can get — more revenue, more margins and so on.
Rationale number two is that it's really the right thing to do. What I mean by that is the solar materials that we're getting and extracting, they're highly specialized solar materials. For example, the glass solar panels, depending on the type of panel it is, by weight or mass is 70% to 90% glass. That glass is highly specialized, and when we extract that glass and sell it back into the glass recycling market, it just ends up getting used for making bottles, for example. That is a waste of a very particular high-quality glass, so the right thing to do from an environmental standpoint, and just a supply chain standpoint, is to remanufacture those materials into finished products.
The reality that we fit in today is the infrastructure for remanufacturing those just doesn't exist in the United States. All of it is done overseas. So as we start to build a domestic solar industry here again with solar panel manufacturing, we need to make these products here domestically, because currently they're all being imported from Asia.
Your co-founder, Jesse Simons, had previously said that you would be able to sell back glass to new solar panel manufacturers once you reach an appropriate volume. How far are you from achieving the volume?
If we talk about using 100% glass that we get to make, we are realistically anywhere between three to five years — and probably closer to five years — away, because of the scale and size you need for running an efficient glass factory. But if we blend and make blended glass, meaning using recycled feedstock that we're getting with some virgin materials, we are only a couple years away from being able to do that in meaningful volumes.
So is the plan that you're going to use blended glass?
To start with, yes, and then over time increase that toward that 100% recycled goal. Typically, for running a basic glass factory you need about 200 tons per day for 100% recycled as the baseline. We're just starting and ramping up our volumes right now, but in the next 12 months we will be getting approximately a third of that.
You charge about $18 per panel for recycling. A study from the National Renewable Energy Laboratory found that anecdotally, recycling solar panels costs anywhere from $15 to $45. How are you keeping costs at the low end of that scale?
Just to be clear, that $18 on average we charge, that includes our freight costs. We charge a single price to the customer, and we handle all the freight and logistics. The way that we are able to [keep prices low] is really twofold.
The first is, the traditional way that people “recycle” solar panels is they're using standard e-waste or electronics recycling equipment and putting solar panels through there. That is a very expensive thing to do, and very non-optimal, because solar panels are big. If you think about a solar panel versus a cell phone that's going through those shredders and the machines and all of that, it's very expensive.
We've designed a very unique set of recycling lines that's optimized and cost-optimized for specifically just solar panels, so it allows us to achieve a level of cost efficiency through that process. As part of that, it's a volume game. The more volumes we can get, the lower the cost of the recycling. We're running only solar panels through and nothing else, so it allows us to achieve an economy of scale that reduces costs.
Thing two is, we're getting way more value out of the panel than any traditional recycler that's doing it today that NREL is looking at. Those recyclers are not extracting and getting any value from the glass, they're not getting the metals out, like silver, because those are challenging to get. That's what our technology does. So we're able to extract more value and get more value in the marketplace so we don't have to charge as much for that takeback handling fee.
Your prices can still be higher than just landfilling a panel. Are you concerned that could exclude you from competing in the market?
What we are working on is that you will not see us charging that same takeback fee five years from now. Our plan, and what we've communicated to customers, is we will be reducing that. The way we will be reducing that is doing two things. One is, obviously, just getting costs down through engineering and scale. And second is getting more and more value extracted out of the panels so we can keep reducing that takeback fee.
Our goal is over the next decade, as these volumes grow, we will be at or near the cost of landfilling. Most of our customers, who are these big solar asset owners, they recognize that today they are paying a premium to recycle with us versus landfilling. But if they work with us and give us the volumes, that's going to allow us to lower the cost.
By the time there are larger volumes of panels, where they're decommissioning and repowering old solar power plants, we will have a very cost-effective recycling process that can compete with landfilling costs, which are only going to go up over the next decade.
A strategy that has succeeded in increasing solar panel recycling rates in Europe, per NREL’s 2021 report, is extended producer responsibility laws. Would you support EPR legislation at the state or federal level for solar panels in the U.S.?
Generally we don't, and a lot of people are surprised by that. As a recycling company, you would think we would want EPR that would force recycling. I think there could be a place and time for it; I don't think now is the time and place for it.
Because what happened in Europe is, if you look at the details of it, all that's required is you need to recycle 85% by weight of the panel. In order to comply with the EU regulation, you have to basically strip off the aluminum frame, which is relatively easy to recycle, and you can strip off some copper cables, and you can shred and crush the rest and use it for asphalt filler. That's what recycling in Europe today is. It's low-value recycling, and because it started that way and the pricing of recycling was set that way and because you can comply, it has killed all innovation.
Today, Solarcycle is a one-year-and-three-month-old company, and we're doing way more advanced recycling for solar than anywhere in Europe today. [EPR] stifles innovation, so it became a victim of its own success. Over time, it is important to recycle these panels. There may need to be laws that come in over the next few years. But we're actually working with the industry, with the asset owners, with the manufacturers to do it in a way that can promote advanced recycling, as opposed to low-value recycling, which oftentimes happens in the EPR situation.
There's a lot of funding for the solar industry coming from some of the big climate bills that we've seen of late, including the Inflation Reduction Act most recently. Do those laws present any opportunity for the work that you do and for solar panel recycling in general?
Absolutely, there are some direct benefits that we're getting. In fact, the Department of Energy just announced some R&D grants, of which we were one of the recipients — about $1.5 million to further develop our recycling technology. There are also tax credits for manufacturing and recycling in the bill, which we will be able to take advantage of to reduce some of the costs of recycling and remanufacturing the materials, because those can get capital intensive.
The real big strategic move in that is the incentives they have for domestic manufacturing of solar cells and solar panels. That's accelerating and spurring a solar manufacturing industry and ecosystem in the United States. That ecosystem is going to need materials, and it's going to need glass and aluminum frames, so the materials that we're getting from the recycling process become more and more valuable and pertinent for that scale-up in infrastructure and domestic manufacturing. It really sets a great stage for these materials and putting them back into the supply chain here in the U.S.