As solar energy booms in the U.S. with record investments and installations, a wave of technological advancements is set to transform the amount of energy solar can produce, where it can be deployed, and how long it can last.
“It seems like when there’s a good idea, it can very rapidly get rolled out through the whole industry,” said Chris Deline, a research engineer who leads the National Renewable Energy Laboratory’s photovoltaic field performance group.
Over the last five years, Deline said, the industry “entirely switched over” from aluminum back surface field solar, or Al-BSF, cells to passivated emitter rear contact, or PERC, cells. “And it seems like there are new emerging entrants within n-type silicon that are poised to do the same thing,” taking over from PERC, he said.
For example, the solar industry is now beginning to make a switch from p-type PERC to n-type tunnel oxide passivated contact, or TOPCon, cells. N-type cells have their wafers doped negatively using chemicals like phosphorus, while p-type cells are doped positively. Doping is the process of adding an impurity to the semiconductor to increase its ability to conduct electricity.
In the early days of solar technology, installations were limited to space applications like satellites, and p-type cells proved more resistant to radiation and degradation in space than n-type cells. This allowed p-type technology to stake out a larger market share early on, and this domination continued after terrestrial solar installations began — though n-type cells are more efficient and resilient for utility and other applications outside of space.
Now, n-type cells are gaining ground.
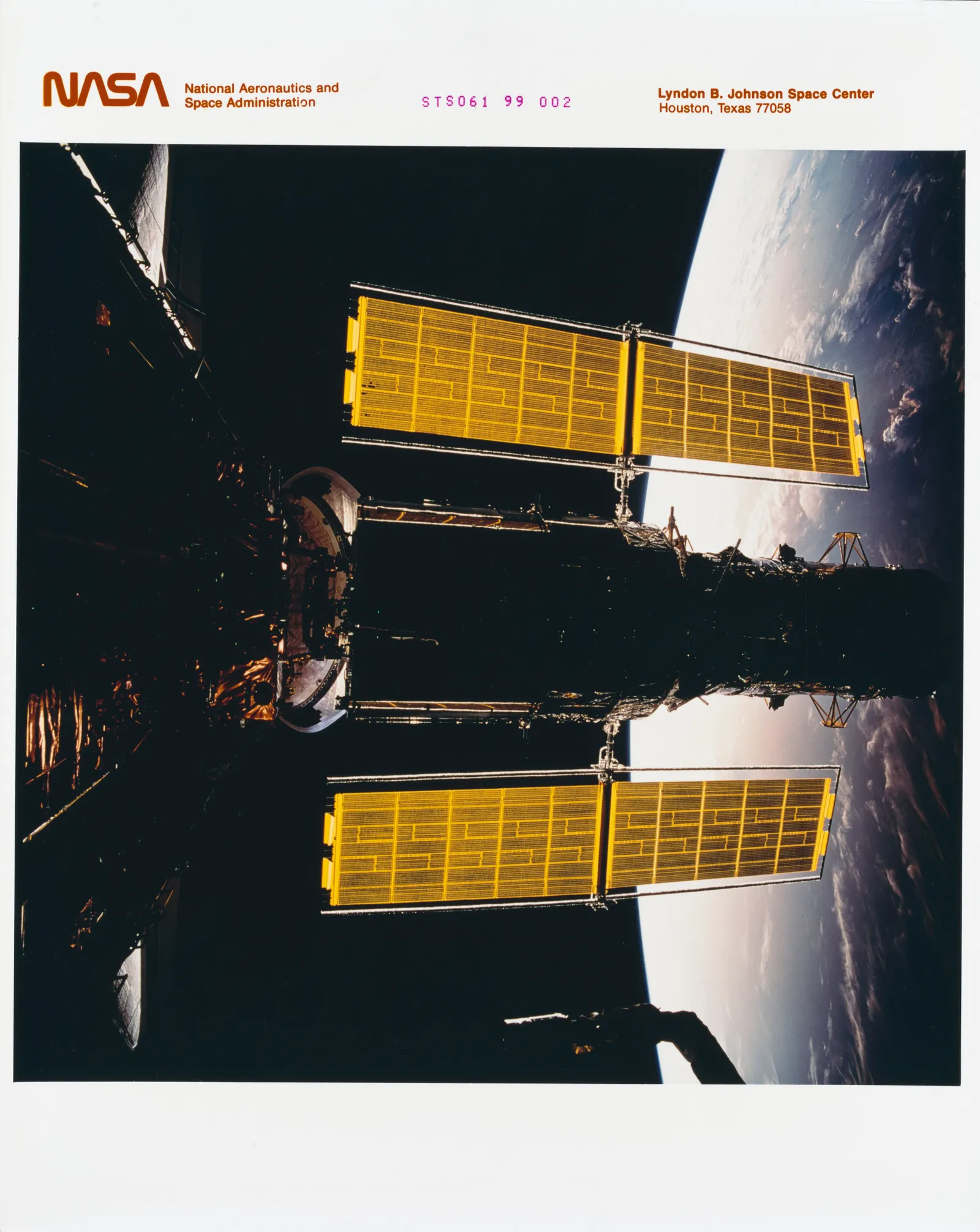
“That's going to be a big transition,” Deline said. “It’s like Moore's Law of faster and faster computer processors that allows them to keep going to higher and higher efficiencies.”
PERC continued to dominate the solar panel market in 2022, but experts predict the technology will go the way of its predecessor, Al-BSF. The German industrial association VDMA said in an April report that it projects TOPCon’s market share will increase from around 10% in 2022 to as much as 60% globally within the next decade, and become the dominating cell type after 2025.
“It is a generally accepted view that TOPCon will ramp up relatively quickly in market share and likely dominate crystalline silicon solar technology in the not-so-distant future,” said First Solar's Chief Technology Officer Markus Gloeckler.
Across all panel types, the average dollars-per-kilowatt cost of solar construction has fallen by a few thousand dollars since 2013, and fell 6% to $1,561 per kW in 2021, the Energy Information Administration said in an October analysis.
What makes up a solar cell?
While Gloeckler sees a bright future for TOPCon, he says First Solar is “confident” in its commitment to thin film technology in the form of cadmium telluride, or CdTe, which is the most popular panel technology for utility-scale deployments — while crystalline silicon panels like TOPCon continue to dominate overall.
The company is set to deploy production of its proprietary copper reduction technology CuRe in the second half of 2024, which Gloeckler said the company expects “will be able to compete very well with TOPCon” due to its “anticipated lower degradation rate” when exposed to high temperatures and humidity.
Gloeckler said the company is also optimistic about its ability to harness the potential of perovskite solar cells, which are “fundamentally thin film semiconductors.”
Perovskite cells have made recent leaps in efficiency, but remain tricky to deploy at commercial scale due to the chemistry presenting stability issues.
In comparison to silicon, perovskite is “relatively inexpensive,” Deline said. “Fundamentally, though, the fact that it's so easy to make may be part of why it's so hard to get it to be stable.”
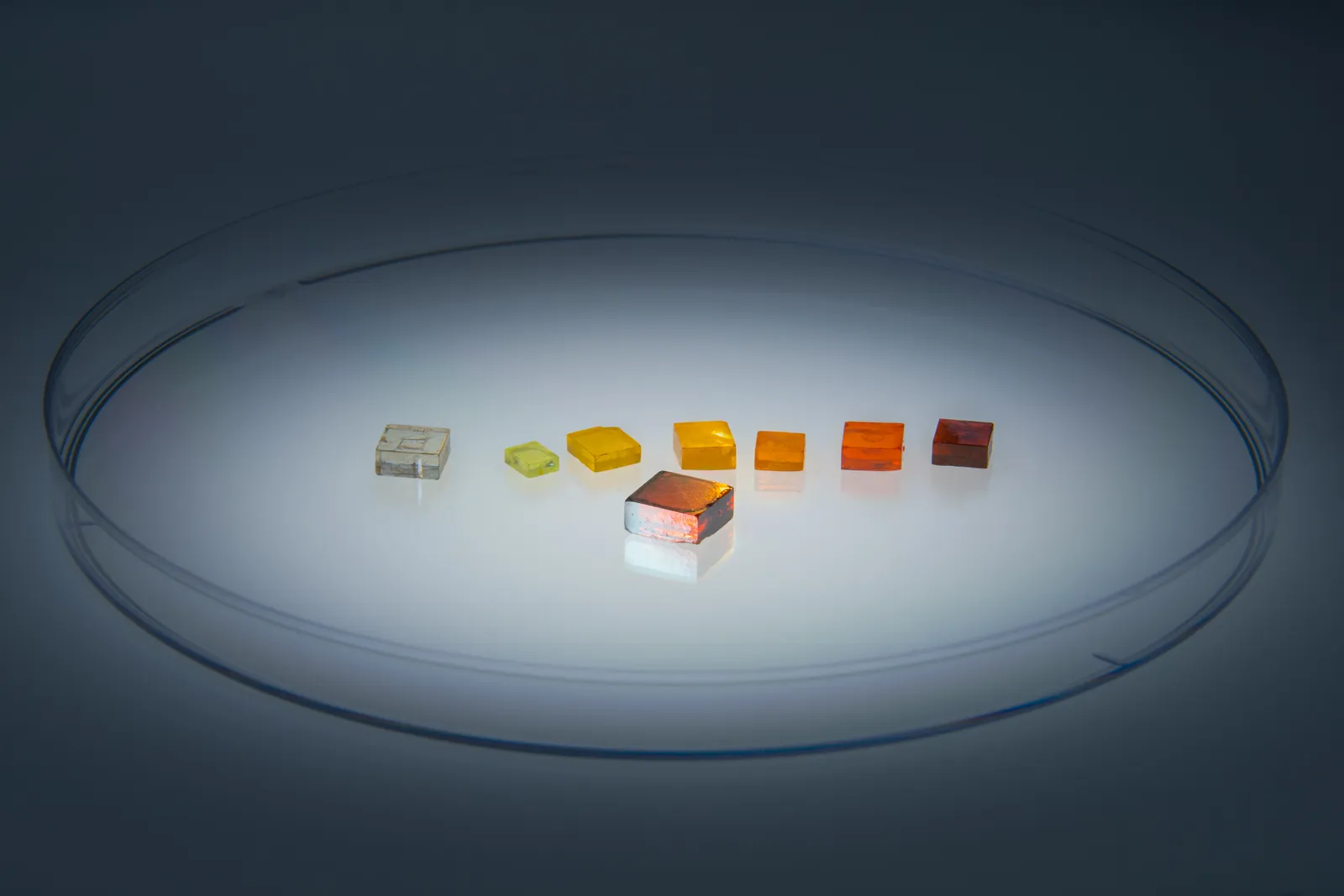
First Solar and its competitor Hanwha Qcells both made investments this year in perovskite-based tandem cell technology. First Solar acquired Evolar, a Swedish start-up focused on tandem cells, and Qcells announced a $100 million investment in a tandem-cell production line.
Tandem-junction cells offer “a path toward higher module efficiencies over single-junction designs,” according to NREL. Multiple junctions — or boundaries between layers of semiconducting materials — allow solar cells to break through the Shockley–Queisser limit, a theoretical limit which prevents single-junction cells from absorbing more than 30% of the solar energy that shines on them.
But researchers are still pursuing higher efficiencies with single-junction cells.
NREL announced a single-junction efficiency breakthrough on Oct. 25, reaching an efficiency of 27% with a gallium arsenide cell. In a release, the lab said researchers optimized the doping and structure of the top layer of the cell to minimize the negative impacts of defects.
Bifaciality, or the ability of a solar cell to produce energy when illuminated from either side, is another cutting-edge innovation. One significant trend Deline sees across the solar industry is “bigger and bigger modules,” which make it easier to reap the efficiency gains of bifaciality.
“You can buy a 630, 650 watt module now, and that's just because [the module] is massive,” he said. “In a lot of cases, these include two layers of glass on the front and the back,” increasing bifacial gain on the back side of the panel where there is “clear glass instead of a white polymer sheet.”
Garrett Nilsen, deputy director of the U.S. Department of Energy Solar Energy Technologies Office, said other areas for innovation in solar panel manufacturing and deployment include different ingot and wafer types, wafering techniques and cell structures, or module architectures, along with cheaper, simpler and more resilient racking systems.
“This is a great time to be involved with solar technology,” Deline said. “There's a lot of innovation going on, and there's a lot of new investments.”
Where can solar panels deploy?
As the technology behind solar cells undergoes rapid innovation, researchers are also working to expand how and where installations are deployed.
DOE projects that the U.S. will need to install 1 TW of solar capacity by 2035 to meet its decarbonization goals, which will require “more diversity of siting configurations,” the department says.
Floating solar is relatively common in Southeast Asia and Europe, but so far has only been deployed at a small scale in the U.S., said Juan Gallego-Calderon, a clean energy engineer at Idaho National Laboratory, or INL. These deployments have been limited in size to around 10 MW, and sited in manmade water bodies that aren’t federally regulated.
Gallego-Calderon is working on an INL project to accelerate the deployment of floating PV in reservoirs that are controlled by federal entities like the U.S. Army Corps of Engineers, the Bureau of Reclamation and the Federal Energy Regulatory Commission.
“The reason why there hasn't been any deployment in those is just because the regulations are not in place,” he said. “So we are investigating the regulatory and environmental pathways, and we’re producing a techno-economic assessment tool that also includes environmental modeling.”
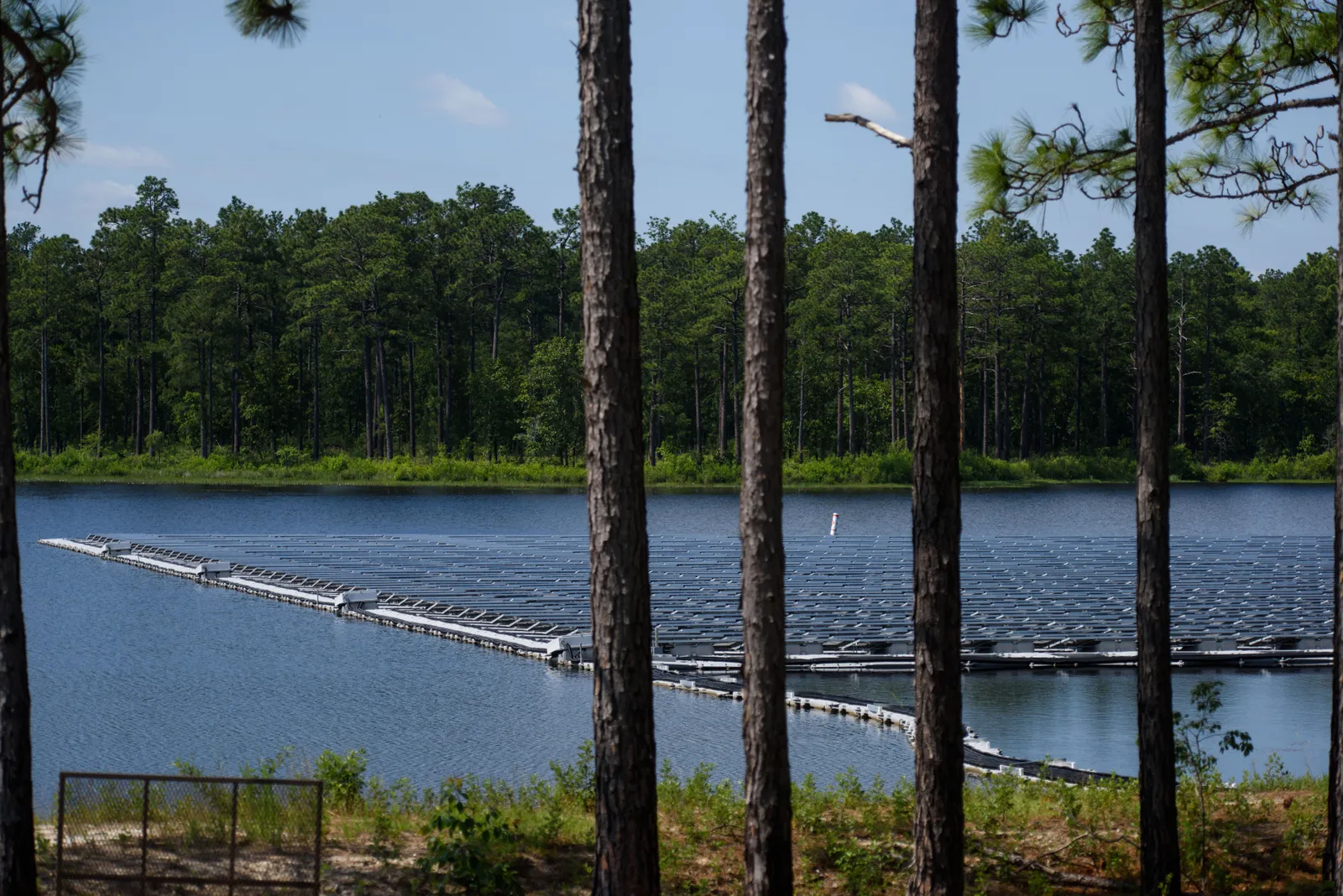
The largest floating solar installation in the U.S. is an 8.9-MW array in the Canoe Brook reservoir in Short Hills, New Jersey, which is owned and operated by the utility New Jersey Resources.
Floating solar in federal reservoirs can help avoid conflicts over land use — such as opposition to solar installations as “eyesores” — and siting it in a hydroelectric reservoir to create a hybrid system can reduce solar curtailment, NREL found in a 2022 report.
“We're looking at a proposed pumped storage hydro facility where they’re actually working with a company to design a floating PV system to put in the upper reservoir to operate in conjunction with the pumped storage hydro,” Gallego-Calderon said. “And they're working on the license right now to submit to FERC, so things are happening.”
Is sustainable recycling possible?
The INL and First Solar are also collaborating to develop a more sustainable recycling process for CdTe panels, participating in a project led by the University of Kansas.
“About half of the utility-scale solar projects are using these tellurium-based thin film solar panels,” said Daniel Ginosar, group leader of the chemical systems group at INL. “The lifespan of those [is] typically twenty years until they start losing efficiency.”
There are also supply chain considerations. As the U.S. aims to deploy massive amounts of renewable energy, the Biden administration has announced a goal of reducing reliance on China for critical minerals, including tellurium.
“We wanted to understand how we can recover the tellurium to reuse it in new solar panels, and at the same time reduce the amount of waste that's going to be generated by the systems coming out of use at end of life,” Ginosar said. Currently, recycling CdTe panels is “not a complete process.”
The existing technique involves trying to break the polymer bonds in panels by crushing them into powder and attempting to leach the cadmium and tellurium from that powder.
The researchers came up with an alternate process of using an ultrasonic mixer to enable fluids like liquid butane to melt the polymer bond, which makes it easier to retrieve the cadmium and tellurium.
Ginosar estimates a “tremendous” buildout of solar capacity over the next 10 to 20 years, though between now and then, solar panels won’t be coming out of service quickly enough to supply materials for the new panels being made.
“But by 2050, those [new] panels will be reaching their end of life, and that's when we can really make a big difference with recycling,” he said.
This particular project is only focused on CdTe panels, Ginosar said, but the researchers are looking to expand the method to “all different types” of solar panels, both thin film and silicon-based.
“We’re just barely getting started, the funding has only just shown up,” he said. “In the short term, it's hard to recycle your way out of the problem. But in the long term, we can be relatively sustainable and be able to recover the tellurium effectively, and completely eliminate the need for mining it from China.”