The urgently needed modernization of the U.S. power system is being impeded by slow access to vital new electric transformers.
Advanced computing and economy-wide electrification are expected to grow demand almost 16% by 2030, increasing the need for both more and bigger transformers, according to a December National Renewable Energy Laboratory study. And that need is being accentuated where extreme weather events like the Los Angeles wildfires and East Coast hurricanes require rebuilt distribution systems.
But global supply chain disruptions continue to slow access to the transformers critical to stabilizing power system voltages and efficiency.
“Delivery of a new transformer ordered today could take up to three years,” said National Association of Electrical Manufacturers, or NEMA, Director of Government Relations Peter Ferrell. “Five years ago, that wait time was four to six weeks.”
Faster access to transformers will take time and investment, manufacturers said.
“The short term appears to be painful for the large investment areas” and “projects have been postponed one to two years already,” said Jeffrey DeSain, general manager, North American Transformer Business, for manufacturer Schneider Electric. “It will take a variety of investment de-risking solutions for supply chains and manufacturers to catch up.”
Load growth pressure on existing infrastructure will likely continue for years, and perhaps for a decade or more, manufacturers and analysts say. Meanwhile, transformer supply solutions, like standardizing transformer designs or organizing and funding a reserve supply, will take policymaker cooperation, if they can be implemented at all, many said.
More than 80,000 types of transformers
There are differences in lead times for the many different types of transformers that step up and step down voltages throughout the power system.
At wind and solar projects, small pad mounted transformers step up voltage to medium or larger sized transformers at production site substations, according to Doug Wolken, Hitachi Energy head of marketing and sales, transformers, North America. Large transformers at natural gas, nuclear, and hydropower plants also step up voltage to the transmission system, he said.
At distribution substations, large pad-mounted transformers step down voltage from the transmission system to medium or small pad mounted transformers, Wolken said. Small pole mounted or pad mounted distribution system transformers step the voltage down for homes and businesses, he said.
The U.S. system had 60 million to 80 million distribution transformers in late 2024, and the 2050 need “could increase by up to 260% compared to 2021 levels,” NREL reported. About 55% of residential transformers are near the end of their lives, with many now more than 40 years old, the lab said.
And there are over 80,000 transformer types throughout the U.S. power system, according to the 2024 National Infrastructure Advisory Council, or NIAC, report from industry stakeholders.
Larger transformer lead times range from 80 to 120 weeks, according to a Wood Mackenzie, or WoodMac, April report. Special electrical steel vital to transformer power loss reductions remains expensive and difficult to obtain domestically, WoodMac said.
Individual manufacturer slowdowns vary. Lead times for pad-mounted distribution transformers “are double or triple” what they were pre-pandemic, said Hitachi Energy’s Wolken. “Transmission scale unit lead times are now three years to six years, with specialized transformers taking the longest time,” he added.
Puget Sound Energy is seeing longer lead times for some equipment, confirmed Andrew Padula, a utility spokesperson, said.
And “realistically, those lead time increases are not expected to improve in the near term,” because their causes are amplifying, WoodMac Senior Analyst, Supply Chain Data and Analytics, Ben Boucher said.
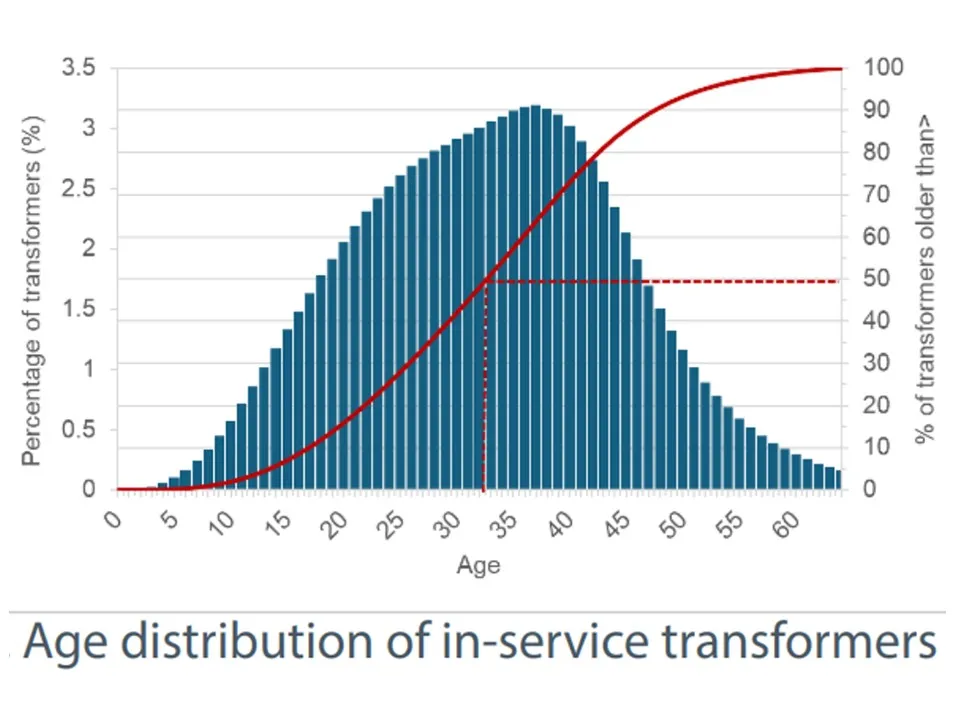
What drives growing transformer demand?
Continuing load growth, aging system infrastructure and worsening extreme weather events are driving the need for transformers, manufacturers and analysts say.
The current shortage began during the COVID pandemic with manufacturing shutdowns and the slowing of global supply chains, Xcel Energy spokesperson Kevin Coss said. Numerous factors continue to drive transformer demand higher, he said.
“We're approaching a time of unprecedented demand for transformers,” Senior Researcher and Distribution Edge Group Manager Killian McKenna, author of an NREL study on transformer supply. Growing electricity demand is straining infrastructure that is approaching the end of its life, from “renewables, data centers, and building and vehicle electrification like EV charging stations and heat pumps,” McKenna added.
Extreme weather events like hurricanes and wildfires impose further distribution system transformer losses, McKenna said. Replacement needs exceed utility inventories to meet everyday failures and new customer requests, according to McKenna.
Following hurricanes Helene and Milton, Duke Energy needed to replace about 16,000 transformers, according to its November earnings report. That is more transformers than other utilities require in a year, WoodMac’s Boucher said.
The rebuilding in Los Angeles has not really begun, according to city officials. As of February 2, Southern California Edison crew members, contractors, and mutual-assistance partners have installed nearly 400 transformers in the Eaton and Palisades wildfire areas, Jeffrey Monford, the utility’s spokesperson, reported.
Soon there will be “enormous new electricity use in bitcoin mining, training artificial intelligence and quantum computing, reshoring U.S. manufacturing, and system modernization initiatives,” said NEMA’s Ferrell. Demand has “catapulted exponentially on a system with a manufacturing base and supply chain sized to meet the market of five years ago.”
The boom in virtual power plants composed of distribution system resources, could reduce system strain, according to developers. But significant added load from electric vehicle charging or electric heat pumps could require larger or more distribution transformers, Scheider Electric’s DeSain, NREL’s McKenna and others said.
After a 2022-23 delayed reaction to growing transformer demand, manufacturers announced $600 million in new transformer capacity investments in 2024, WoodMac’s Boucher said. Schneider Electric “is investing hundreds of millions of dollars in capacity expansion,” DeSain added.
Hitachi Energy North America is investing $500 million in transformer manufacturing capacity through 2027, said Wolken. This is part of a $1.5 billion global transformer production investment, which is based on demand expected to be sustained for at least 10 years, he added.
But that investment may be inadequate to meet demand, and other more innovative solutions have been proposed, manufacturers and analysts said.
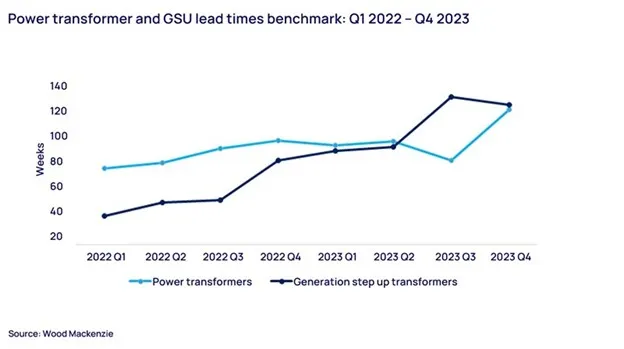
Solutions to transformer shortage
Of seven solutions described in the NIAC report, three are already being used by manufacturers, utilities and other stakeholders.
More accurate demand forecasting and longer-term agreements between electric companies, manufacturers and suppliers of raw materials like electrical steel are already in practice, said Edison Electric Institute, or EEI, Senior VP, Security and Preparedness, Scott Aaronson.
Utility resilience planning against extreme weather events has led to “storm stock” inventories, which are in-house supplies of distribution system infrastructure, according to Aaronson. “Big utility companies may have access to large power transformers and 10,000 or more distribution transformers through mutual assistance networks,” he said.
Integrated planning has allowed anticipating when and where transformers will be needed and partnering with manufacturers to ensure supply, said Xcel’s Coss.
“Until recently, few utilities, manufacturers and supply chain partners had strategic alignments, but five-year projected plans and long-term agreements are becoming the norm,” said Schneider Electric’s DeSain. “A multi-year view and choosing more standard designs, materials and electronics can mitigate risk,” he added.
“Replacing aging infrastructure can be a massive opportunity or a lost opportunity,” NREL’s McKenna said. “Near term decisions that don’t anticipate future load growth and the growing need for resilience will impose high labor costs,” but building for long-term needs can be an opportunity to make them one-time costs, he said.
The NIAC report’s call for federal policy and funding support for expanded transformer production will come before the 2025 Congress as the just released Moran-Cortez Masto bill.
“Extending the federal 45X tax credit for domestic manufacturing would support more U.S. transformer production,” NEMA’s Ferrell said, adding that “state or federal initiatives that grow the workforce could be the best policy solution because automated manufacturing of so many unique types of transformer and transformer components is not plausible.”
The NIAC report also proposed a virtual transformer reserve with the U.S. government as the buyer of last resort.
“The reserve would not be a physical stockpile, but a way to retain spare manufacturing capacity,” NEMA’s Ferrell said. “It would be a commitment to sustain medium to long term manufacturing capacity certainty, but it is not clear how to determine the needed federal investment and who would provide it and how to manage the reserve.”
There would, however, be little risk because current demand growth seems to be long term, Aaronson said.
The NIAC report’s most important proposal might be standardizing transformer design.
Standardization “would make it easier to share equipment and to produce more transformers faster to meet the growing demand,” EEI’s Aaronson said.
But because of the many types of transformers, “it may not be possible to significantly reduce production times,” said NEMA’s Ferrell. Utilities could agree on standard specifications, “but that will be difficult because a newer utility in Southern California will have very different operational needs than an older Maine utility,” he said.
Schneider Electric’s DeSain and Hitachi Energy’s Wolken agreed. The U.S. power system “is one of the most novel machines in the world, with transformers designed and manufactured to very specific local distribution system intricacies, which makes standardization a real challenge,” Wolken said.
On average, for every 1,000 transformers on a distribution system, there would likely be 200 or more different transformer designs, according to Wolken. “But there may be areas where, with utility leadership, some level of standardization is possible,” he said.
Even if transformer variation was reduced from 80,000 types to 60,000 types, “it would allow a little more efficient manufacturing process,” said EEI’s Aaronson.
Standardization may seem complicated, said WoodMac’s Boucher. But when a severe weather event occurs, utilities “take whatever transformers they can get, which suggests standardized specifications and designs are realistic and can be a key to resolving current shortages,” he added.